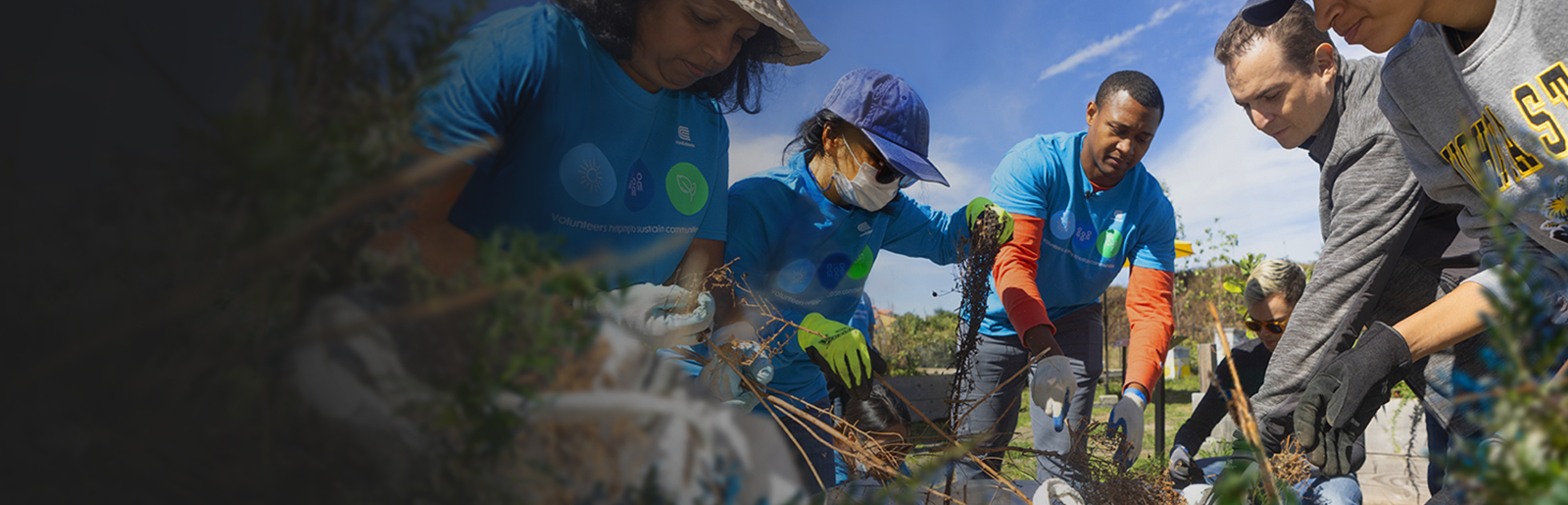
Embedding Health & Safety
into Our Culture
Employee Health & Safety
At Consolidated Edison Company of New York, Inc. (CECONY) and Orange and Rockland Utilities, Inc (O&R) (together, the Utilities), our top priority is the safety of our employees and the public. Safety is engrained in the way we work, and we remain committed to embedding safety as a core principle of our culture. Consistent progress is essential to achieving our goal of a zero-harm workplace. At CECONY, injuries have reduced by more than 68% since 2009. In 2022, CECONY experienced one significant high-hazard injury and concluded the year with an injury and illness rate of 1.23, which was higher than the target of 1.00. O&R improved upon its best injury and illness rate again in 2022, achieving a rate of 0.53. O&R had one significant high-hazard injury last year and has seen a 90% reduction in injuries and illnesses since 2009.
Key focus areas for sustained improvement include:
- Promoting a first-class safety culture by making safety personal and the focus of every task, every job, every day
- Programmatic focus on areas of concern within the company and industry, such as hazard recognition and mitigation, soft tissue injuries, and slips, trips and falls
- Closing gaps to prevent injuries by identifying and addressing unseen hazards
- Preventing injuries by re-invigorating our Close Call program and promoting our new mobile application for submissions
- Encouraging safety leadership through training, mentoring, and technology with the accelerated adoption of the Safety Leadership System
- Using and developing tools by leveraging data from job briefings
- Training employees on driving safety and slips, trips, and falls conditions through simulations
- Working towards 100% procedural compliance to support a zero-harm workplace
The Utilities’ focus on cultivating a zero-harm workplace drives their initiatives to instill a safety conscious mindset in all employees and reduce incidents. At CECONY, there were 157 recordable injuries and employee illnesses (138 injuries and 19 illnesses, respectively) in 2022, which was the third lowest number of injuries and illnesses in its history. At O&R, there were six recordable injuries, which was also a historical best. The Utilities’ efforts have resulted in an estimated reduction of more than 6,000 injuries since 2009.
Notable recent efforts include the Unified Safety Council, which is a group of senior leaders across all operating divisions that will serve as a governing body to develop, vet, and implement consistent company-wide safety initiatives, programs, and best practices. The first focus area included Supervisor Safety Training. Another effort included the launch of a Daily & Routine Ergonomic Stretching Program to mitigate soft tissue injuries and establish a consistent full body warm up exercise to advance the premise of the Industrial Athlete. To date, over 400 company personnel across all operating organizations were trained to champion and lead “Body Inventory” stretching for both field and office groups. Approximately 8,000 employees have participated in reoccurring stretch sessions led by ergonomics-trained specialists. In 2022, CECONY established a Close Call Recognition Program to acknowledge and reward quality close call submittals that help prevent incidents, increasing the amount of submissions by over 60% from 630 in 2021 to over 1000 in 2022.
Since 2009, injuries have reduced by more than 68% at CECONY.
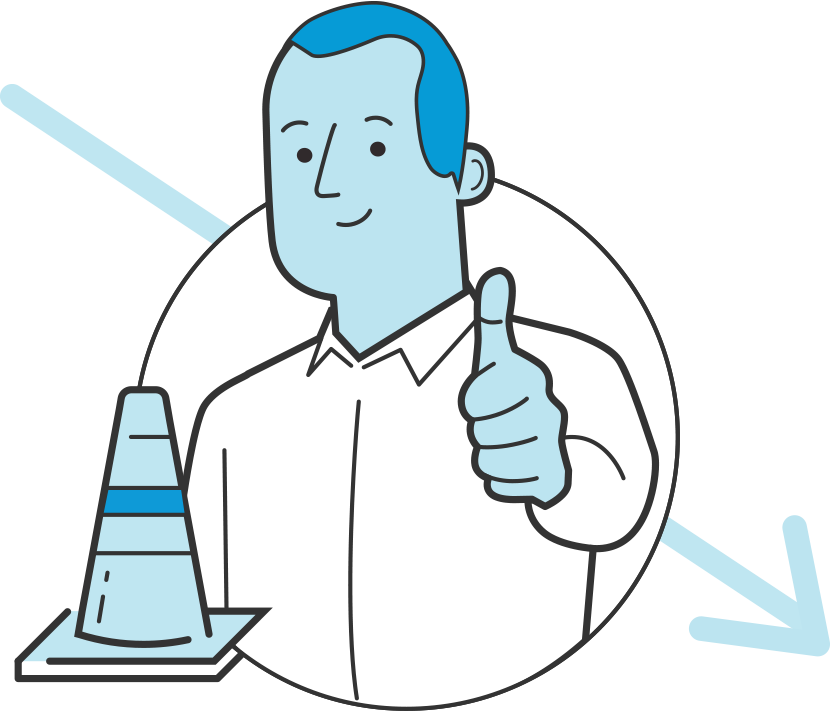
At CECONY, critical safety programs are maintained as corporate procedures to codify our proactive approach to safety. An essential safety practice is delivering Job Briefings. As outlined in a corporate instruction, job briefings must be conducted for each job and are required to be complete and robust reviews of the scope of work, including a discussion of any hazards associated with a job. Our Job Site Safety Exchange, Job Safety Analysis, Close Call, and Time Out programs are other examples of programs that help us identify and mitigate safety risks.
Auditing plays a critical role in providing a field presence and supporting the company’s goal of a zero-harm workplace. Internal Auditing has a dedicated Environment, Health and Safety (EH&S) department. The group conducts two types of unannounced audits: EH&S compliance audits at facilities (such as administrative buildings, service and operation centers, generating stations, substations) and EH&S compliance inspections of employee and contractor crews working in the field. Internal Auditing also performs process reviews of various EH&S programs such as the Hearing Conservation Program, Respiratory Protection Program, Close Call Program, Spill Prevention, Control & Countermeasures, vehicle idling, spill reporting, remediation, waste management, and more. The annual audit plan includes a balance of each of these audit types.
In addition to the multitude of corporate procedures and instructions we maintain to support our health and safety program, we have safety-specific targets that we assess regularly. We track and report on our OSHA Injury and Illness rate on a monthly basis on both a corporate and departmental level. We also track our motor vehicle collision rates by collision type, helping us improve the efficacy of our driver safety programs. Over the past few years, we have developed the Safety Leadership System (SLS), which takes a data-driven approach to safety. The SLS enables us to view our safety performance from the corporate level all the way down to the smallest working group or individual.
Con Edison of New York OSHA Incident Rate
- Rate
In addition to many of the previously mentioned programs, O&R continues its progress toward a zero-harm workplace thanks to the joint union-management Corporate Safety Committee, Company Safety Team, and 12 organization-specific safety teams. In 2022, these teams collaborated to develop very specific driver training for our employees based on historical performance, learning opportunities while reviewing incidents and other industry experiences regarding motor vehicle collisions. The diversity of these teams strengthens our efforts and support from our employees. Our daily warm-up program has continued to demonstrate success; we have decreased our soft tissue injuries by 90% and our days lost due to soft tissue injuries by 95% since the inception of the program. Our communications program has been lauded by our users for its quality and timeliness. Our communications program incorporates lessons learned from our industry and peers, root cause analysis results (from injury and collision reviews), close call reporting, and other measures that have also boosted our overall performance.
Orange and Rockland OSHA Incident Rate
- Rate
Contractor Health & Safety
It is company policy that our contractors comply with all applicable laws and Con Edison procedures or requirements. Our policies require that we procure, manage, and evaluate suppliers based on their environment, health, and safety performance. Contractor training is reviewed during the qualification process. We offer additional training for contractors at our Learning Center, if necessary. Contractors seeking to be qualified to perform field work must provide an Environmental, Health and Safety Plan (EHASP) detailing how they will comply with all environmental, health, and safety standards that apply to the work that they perform. EHASPs that simply restate the regulatory standards are not acceptable. Company field inspectors oversee contractor work and are responsible for confirming that contractors are working in accordance with all applicable standards. If the supplier’s work fails to comply with the contract requirements, field inspectors must take immediate corrective action. A Contractor Field Observation Report, Infraction Report, or Action Line must also be filed in our Contractor Oversight System. In addition, contractor safety performance is tied to some of our Key Performance Indicators.
Our Contractor Compliance Committee
Additionally, CECONY has an established procedure for cases to be referred to and considered by a cross functional Contractor Compliance Committee, to review alleged violations of the Vendor Code of Conduct – Values and Guidelines for Vendors (the Code), contract terms and conditions, and any other allegation of unsatisfactory performance by a contractor. The Committee will meet as required to evaluate allegations, review the findings of investigations, and address matters arising in the Contractor Oversight System. The Committee will jointly determine any corrective action or discipline required of the contractor. Additionally, the Committee may apply one or more disciplinary measures, depending on the seriousness and severity of the violation and the contractor’s previous performance. These actions include, but are not limited to, suspension from the current project or contract, suspension from future bidding, cessation of all work performed by the contractor as a prime or subcontractor, monitoring by a third party, application of a bid multiplier, cancellation of the contract, and removal from the List of Qualified Suppliers.
Contractor Safety Seminars
CECONY’s Construction organization, which oversees the largest share of CECONY’s contractor-executed projects, hosts quarterly Contractor Safety Seminars. The targeted audience for the seminars are owners, principals, executives, and safety leaders of the diverse companies utilized by CECONY to execute work not performed by our in-house labor force. The Seminar agenda(s) cover safety performance, trends, best practices, and lessons learned. Best practices and lessons learned topics are presented by members of the contractor community or local regulatory agencies, creating a collaborative and informative atmosphere for all in attendance.
Identifying and Documenting Improvement Opportunities
Job Site Safety Exchanges are performed concurrently with standard safety inspections by employees overseeing contractor-executed projects for the Company. The observers, through technical understanding of the job activities and associated hazards, discuss and evaluate concepts including job briefing completeness and adequacy in energy source controls, communications, work methods, PPE use, work area setup, and vehicle safety. Improvement opportunities and excellent observations are discussed and documented.
Contract Administration
CECONY maintains a Contract Administration Manual (CAM). The CAM’s purpose is to provide direction for Company personnel in the administration of contracts and in the documentation of contractor performance to ensure the efficient utilization of Company and contractor resources and compliance with Corporate Instructions. EH&S is responsible for providing updates to address new or revised environmental, health, or safety laws or regulations. Among other responsibilities, the CAM establishes that various Company oversight and support personnel are responsible for the following:
- Monitor day-to-day contractor work activities and verify adherence to the contractor’s Environmental Health and Safety Plan (EHASP) and Work Plan.
- Input observations into the Contractor Oversight System
- Only perform environmental tasks after receiving appropriate training (e.g., signing manifests)
- Notify appropriate managers & EH&S representatives of any accidents or unresolved safety problems on site and request assistance when needed
- Use the Close Call Program to report potential hazards, unsafe conditions/behavior
- Use the Time Out Program when an unresolved safety, health, and/or environmental concern arises on a job
- Timely reporting of spill